In today’s dynamic workplace, safety, compliance, and informed decision-making are paramount. A comprehensive understanding of safety data sheets (SDS) is vital for achieving these goals. This article will explore what is a Safety Data Sheet in-depth, covering its definition, purpose, authoring, and key questions surrounding its use.
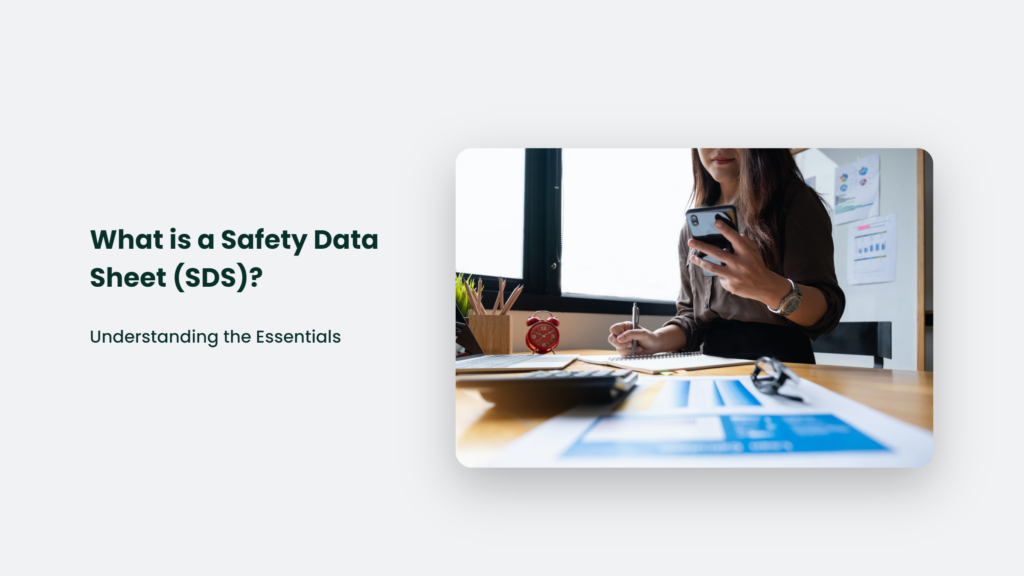
What is a Safety Data Sheet?
A Safety Data Sheet, commonly called an SDS, is a comprehensive document containing 16 sections outlined by the Globally Harmonized System (GHS). It provides detailed information about hazardous chemical products found in the workplace, aiming to ensure the safety of employees and the environment. The SDS offers more extensive hazard information than the product label and instructions on working safely with the hazardous product, making it an indispensable tool for risk mitigation and emergency response.
The Purpose of a Safety Data Sheet
The primary purpose of an SDS is to communicate the hazards of chemical products to ensure safe handling, storage, and disposal. It also provides essential information for emergency responders in case of accidents. By outlining the risks to individuals and the environment, an SDS is crucial in guiding organizations in effectively mitigating these risks.
Who is Responsible for Writing a Chemical Product’s SDS?
The responsibility for writing a chemical product’s SDS typically lies with the manufacturer, importer, or distributor. However, in some cases, the end-user may need to create an SDS, especially when the product is formulated in the workplace.
What Should a Safety Data Sheet Contain?
An SDS should contain a wealth of information, including the product’s properties, physical and health hazards, safe handling measures, and emergency procedures. It must be presented in a consistent, user-friendly 16-section format, as mandated by the Hazard Communication Standard (HCS)
Best Practices for Safety Data Sheet Authoring
When authoring an SDS, avoiding jargon or abbreviations and using clear, concise language to convey information is essential. Furthermore, keeping SDSs updated is time-consuming, given the constant revisions and differing national requirements. Therefore, adhering to best practices in SDS authoring is vital to ensure compliance and safety.
Examples and Statistics
- According to the Hazard Communication Standard (HCS), the SDS must include specific minimum information, such as the properties of each chemical, the physical, health, and environmental hazards, and safety precautions for handling, storing, and transporting the chemical.
- In a recent webinar, EcoOnline Consulting Manager Sarah Ingle and Solutions Consultant Jack Cleaver highlighted common pitfalls in SDS authoring and provided valuable insights on overcoming them.
Frequently Asked Questions:
What are the consequences of not having an updated SDS?
Failure to maintain updated SDSs can lead to non-compliance with regulations, potentially resulting in fines and, more importantly, jeopardizing the safety of employees and the environment.
Can an SDS be in a language other than English?
While the information contained in the SDS must be in English, it may also be presented in other languages to cater to diverse work environments.
The Bottom Line:
In conclusion, safety data sheets are indispensable for workplace safety and environmental protection. Organizations can effectively mitigate risks and create a safer work environment by understanding their purpose, adhering to best practices in authoring, and staying updated on regulations.